The hands putting the jigsaw of a vehicle together have complex job to do.
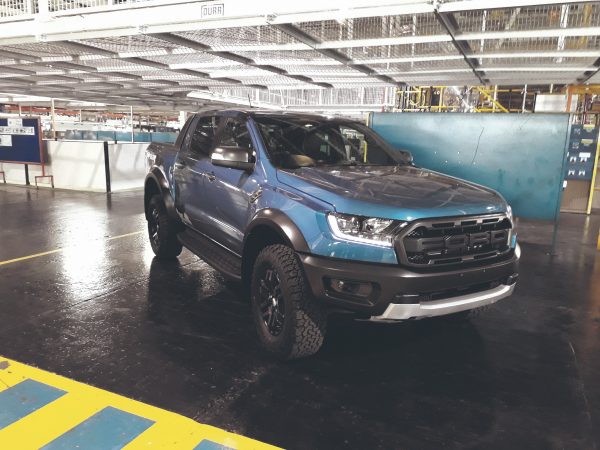
Next time you climb into your car, in fact when you open your door already, try and imagine all the parts under the skin behind the handle pulling the required cable to dislodge the required lock switch, which in turn enables you to swing the door’s frame on the specially crafted hinges.
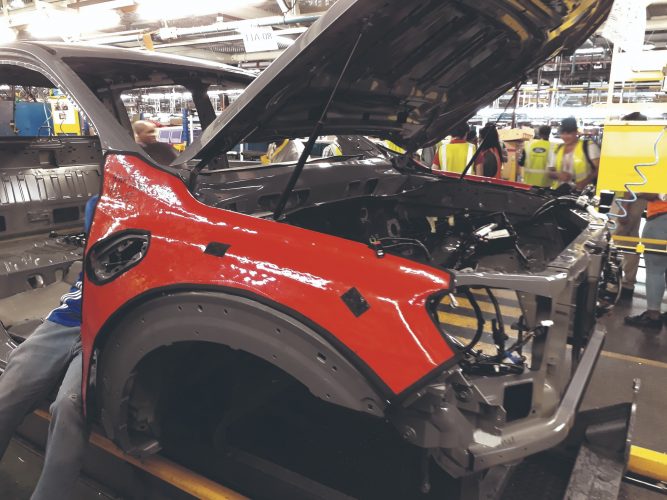
.
Ford gave a group of motoring reporters the unique experience of working on live models in their Silverton plant last week and the only conclusion we could draw was that the hundreds of individuals who put your car together don’t get the respect they deserve.
If the car gets good reviews, the brand’s designer or clever designers get the credit while all the hands that actually put it all together are almost always overlooked.
Trust me, those hands handling the thousands of parts during the birth of a car have a much more complex job to do than the robotic arms on a conveyor belt on which beans get canned.
Ford recently upgraded their Silverton facility in order to build the highly anticipated new Ranger Raptor, in addition to the Ranger and Everest models that were already produced by the plant.
.
Originally being lured into the idea to work on the Raptor models before even being put into action, the media contingent was blown away by the sheer magnitude and gross complexity of the intricate workings of the plant that spits out a staggering 530 cars per day.
After being kitted out with the appropriate gloves, watch protectors, safety vests, boots and goggles, we set off through the myriad of stations and stages of productions to reach our assigned places.
Carefully selected stations, I might add, as there are no guarantees that scribes will be as handy in car production as they are behind a keyboard.
And our initial observation and training were only on Ranger and Everest models in anticipation of the arrival of Raptors, which feature all of 750 unique parts from the Ranger.
.
Very envious of the pairing being entrusted with fitting the Ford badges on the back of the loadbox doors, my job on the right side of bare cabins – which entailed fitting one plastic storage box into the hole under where a back seat was to be fitted later on the assembly line – seemed far less glamorous.
And so easy of course. Align the storage box’s two fixed plastic rivets to the two holes on the cabin body and push through additional rivets once you’ve aligned the other four holes in the storage box through the punched holes in the carpet into the holes in the steel structure underneath.
What does that ad say: “What could go wrong?”
Try fitting the storage box the wrong way around, forgetting to move the rear seatbelt buckle, breaking the two fixed rivets and not lining up the carpet holes with the body holes resulted in numerous broken plastic rivets.
.
So to answer that question: everything that could.
I got the hang of things, but never felt confident I would pass a merit appraisal.
And the scary part was that the fitment of my precious storage box was only one of four parts the person who works in that station does on every passing unit.
She also had to fit a panel between the windscreen and passenger window, a panel over the front safety belt and a panel in the back corner of the cabin over the rear safety belt.
She has to take out the neatly stacked pile from a specific holder, put them in the bare cabin, remove them from their plastic bags, fit them by aligning all the rivets to the holes, press them in, walk to collect rivets for the storage box and fit them; secure all her panels with a rubber hammer and finish by removing the empty plastic bags from the cabin.
.
All of this while the unit passes the start line of her station until it passes over the finish line which initially feels like a few seconds.
And every now and again the line stops and they work backwards as fast as they can because when the line starts again it might make up for lost time.
To think that is only one tiny fitment station on a production line where every vehicle travels for 14km over four different lines before eventually merging into the finished product.
The progress of every vehicle or its various components can be traced by any Ford dealership in the world in anticipation of its shipment status and delivery.
It’s easy to see why vehicles from the Silverton plant get exported to 178 countries.
.
I have new-found respect for all those anonymous people putting together a car from scratch.
They are truly the unsung heroes of the industry.
For more news your way, download The Citizen’s app for iOS and Android.